China Metallurgical Sidi: Promote the new era of intelligent manufacturing in the whole process of steel
Author:China Metallurgical News Agenc Time:2022.08.24
At the 2022 China International Intelligent Industry Expo, which opened on August 22, China Metallurgical Sidi demonstrated an industrial intelligent manufacturing product- "Metallurgical Full Process Intelligent Factory" system solution, which introduced the unity based on China Metallurgical Sidi construction based on the construction The entire process digital steel factory of the Industrial Internet Platform -Shandong Yongfeng Lingang Intelligent Factory.
As the global steel industry's first single -platform full -process smart factory, Yongfeng Lingang Intelligent Factory combines "lean" and "intelligent" genes, allowing the production data of the entire plant to gather on the same platform, and set up a high -quality transformation and upgrading of the steel industry. The new benchmark once again demonstrates the leading position of China Metallurgical Sidy in the field of intelligent manufacturing. As of now, the first phase of the Yongfeng Lingang Intelligent Factory has more than 1,800 industrial models and functional modules. The cost of corporate tons steel has decreased by more than 100 yuan compared with the same caliber, and the per capita tons of steel exceeds 1,500 tons/year.
Yongfeng Lingang Iron and Steel Base Intelligence Control Center
Since the world's first Iron and Steel Smart Collection Control Center built in 2018 has been put into production in Baowu Shaang, China, China Metallurgical Sai has continued to make efforts on the intelligent manufacturing track to promote the new era of China's steel industry to move into the entire process of intelligent manufacturing.
Let the processes and departments achieve no border collaboration
The traditional ISA95 five -level information architecture has the problem of vertical data attenuation and horizontal data islands, and the synergy efficiency is low. The "soil and water cloud" industrial Internet platform independently developed by China Metallurgical Sai Di broke the traditional information architecture and adopted a flat system structure with independent intellectual property rights, allowing the unified industrial Internet platform of the in -depth control layer to directly carry various intelligent applications. This can efficiently collect and process massive data, so that the data can exert its due value.
If it is said that in the five -level information architecture, the information must be transmitted layer by layer to reach the "smart brain" of the data application, then the "water and soil cloud" industrial Internet platform is like the "neural network" of the data of the four links. Roots down at the basic automation level to achieve data access and comprehensive governance of the entire process, full -process, and full elements.
In Yongfeng Lingang Intelligent Factory Project, the full process and full control business of steel production are carried on the unified industrial Internet platform. The platform has access to more than 30,000 processing equipment, and the real -time data exceeds 500,000 points. Since its launch, it has collected and stored 35 billion storage data. The platform opens the data transmission link vertically, runs across the production processes and management departments horizontally, and opens the "black box" of the production process to achieve digital and transparent production, so that the procedures and departments can achieve borderless collaboration.
Yongfeng Lingang Iron and Steel Base Intelligence Control Center
Let the control tubules become unified as a whole
From Shao Gang's first Iron Institute Smart Collection Control Center, to the first hot -rolled steel roll warehouse smart heavy load storage system in Baowu Batang, China, and then to the first smart raw material field of Baowu Zhangang, China, the first unmanned locomotive iron water transportation system, In the first smart water control center of the entire factory, China Microeidi continued to connect to the process of promoting steel intelligent manufacturing. Today, Yongfeng Lingang Intelligent Factory Project has once again created a new model of the intelligent and digitized Chinese steel industry with a unified platform -based full -process intelligent manufacturing.
This project has set up the "Industrial Internet Platform+Intelligent Management and Control Integrated, Iron Area Integration, and Steel Rolling Integration" system architecture, so that the entire process production can not only perform their duties according to the characteristics of the unit, but also achieve a unified dispatch that runs through the entire plant throughout the factory. Essence In this project, China Metallurgical Syedi has developed 12 major types of intelligent applications such as production, equipment, energy, logistics, and Anhuan. It is equipped with more than 1,800 industrial models and intelligent applications. Each link to the finished product has provided digital support, so that the control tube is a unified whole, realizing the digital scheduling of the entire plant and the efficient synergy at all levels, which has greatly promoted the reduction of costs and efficiency of the enterprise.
Taking temperature control as an example, accurate and detailed temperature control is the basis of steady production of steel, and it is one of the important starting points for improving product quality and profitability. The integrated management and control system of this project can track the material temperature conditions of various processes such as iron, steel water, steel outlets, furnaces, refining stations, refined stations, refined stations, etc. based on the model prediction target temperature, and for iron water finger cranes, etc. , Refining heating temperature and so on, provide guidance. The full -process control of rhythm and temperature and other elements achieves efficient collaboration between process interfaces. After the integrated management control system was launched, the enterprise refined power consumption was reduced by 2 kilowatt -kilowatt -hours per ton of steel.
Use data to promote all staff to improve
"Lean" has always been the keyword of Yongfeng's development. In the historical period of lean foundation and lean operation, entering the digital era, Yongfeng accelerated the conversion of kinetic energy, and joined hands with China Metallurgical Sidi to start a new stage of lean intelligence.
The intelligent operation of the entire process not only improves the automation level of production at the operation level, but also provides large -scale data assets for the unified control and coordinated linkage of the entire factory, opening a new space for better production of lean production. Through the window of data, each employee can use the data to move towards the lean improvement goals.
Traditional KPI (key performance indicators) management can often only be controlled to the company and the factory level. The indicators data are offline statistics, afterwards calculations, and there are problems with lagging indicators and insufficient refinement. In the KPI kanban created by China Metallurgical Cydi for Yongfeng, the indicators are decomposed step by step from the entire factory's overall viewing, from the operation area, process, and production line until they are refined to one team. This KPI management system is equipped with more than 600 performance indicators. These indicators are the results of real -time computing, real -time acquisition, and real -time update, which provides accurate and transparent data support for enterprise production decisions. This is a concentrated embodiment of the concept of improving the concept of all employees in the context of the big data of the intelligent factory. Each employee can locate problems in the data and use data to improve. Through continuous improvement, the pursuit of extreme optimization of cost is optimized. From the intelligent manufacturing of a single system unit to creating a full -process intelligent factory, China Metallurgical Sai Di has achieved the first and even the world's first achievements in China with its leading intelligent manufacturing solution. The transformation of the driver has achieved significant results in the aspects of cost reduction and efficiency, lean production, improving labor productivity, and realizing essential safety. It has vigorously promoted the intelligent change of the production mode of the steel industry, reflecting the responsibility of state -owned technology -based enterprises to promote industrial transformation and upgrading Essence
Based on the new era, China Metallurgical Sidi will continue to practice the innovation -driven strategy. By solidly promoting the deep integration of intelligent big data with the real economy, it will continue to create new value for the high -quality development of the steel industry with new methods and new models.
Author | Reporter Tao Haiyin Correspondent Zhou Yan
- END -
Just tomorrow!Ready to watch
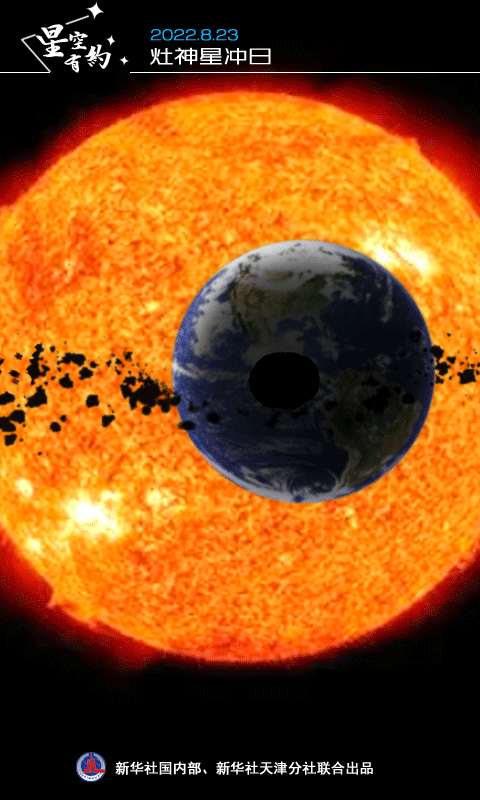
Poster production: Feng JuanAccording to astronomical popular science experts, the...
High -end "Made in Hubei" appearance!Mobile Medicine Imaging Center "Entering" Jianbo Fair
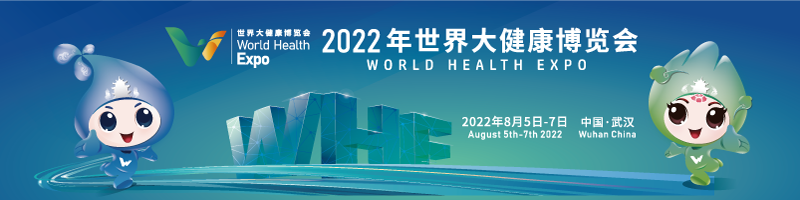
The Yangtze River Daily Big Wuhan Client August 5th News On the morning of August ...