Integrated die -casting fire, and then?
Author:British magazine Time:2022.06.27
The cost saved by integrated die casting is the source of profit for some component companies.
The technology industry has never lacked leaders. Apple's iPhone 4 created the era of smartphones, while Tesla led global electric vehicle frenzy. As the electric vehicle is promoted, the BBA is gradually replaced by BYD and Wei Xiao, and the latter has become the first option for car purchase. However, although the electric vehicle is good, there is always a pain point lingering, that is, battery life.
In order to improve the mileage of battery life, major industrial chain companies rack their brains. Recently, the Kirin battery was released in the Ningde era to mark the 4680 battery against Tesla.
In addition to trying to improve the energy density of the battery, the OEMs also dug out the car production. For example, Tesla successfully applied the integrated die -casting of Model Y mass production, which attracted Weilai, Xiaopeng, and even Volkswagen, Mercedes -Benz, etc., and then set off a wave of capital frenzy in A shares.
01
How good is integrated die?
Behind the choice of capital is the balance of interests.
The traditional manufacturing process of automobiles mainly includes four links: stamping, welding, painting, and total assembly. After pressing alloy plates into different parts of parts, assembled into white body by welding, riveting, glue, etc. (body welding assemblies), and then coating such as anticorrosion, spray paint, etc. Finally, internal and external decoration, power power, power Components such as total assembly and chassis assembly are assembled on the body to complete the whole vehicle assembly.
Since the car white vehicle is composed of hundreds of parts of the shapes and materials, the error of each part will affect the performance and safety of the vehicle. Therefore, the OEM must be strictly tested and controlled the whole process of the design to the packaging logistics of each part and the entire process of acceptance and the rectification of the factory. This increases the cost of automobile production, and the efficiency is not high.
There is also a problem with the weight of the car. According to the relevant data of the International Aluminum Association, the weight of the electric vehicle is positively related to the power consumption. If the weight of the pure electric vehicle is reduced by 10kg, the continuous mileage can increase by 2.5km.
However, although the electric vehicle reduces the engine and gearbox compared with the fuel vehicle, the three -power (motor, electrical control, battery) system is added. The energy density of the battery power system is lower than that of the fuel system. For fuel vehicles.
At the same time, the mileage is the ultimate pursuit of electric vehicles, and the lightweight of the vehicle has become an important option.
With the continuous increase of lightweight demand, aluminum instead of steel to reduce self -weight has become the mainstream choice. The amount of aluminum alloy dosage is gradually increased, and the splicing process of body structure parts uses the original stamping+welding process, which also increases accordingly, leading to rising costs and decline in efficiency.
In this context, integrated die casting emerges.
At the battery day in September 2020, Tesla announced that Model Y will use integrated die -casting rear plate assembly, which will be dotted by the assembly that was originally stamped and welded through components. The cost is therefore decreased by 40%. And after the integrated die casting, the Model Y body weighs 66 kg, which is 10-20 kg lighter than the smaller Model 3. At the same time, parts of parts can better bear the impact when the corresponding collision and improve the safety of the body skeleton.
Not only that, after using integrated die -casting technology, the production process is simplified. While the production efficiency is greatly improved, the required technical workers have been greatly reduced, and the labor costs have also decreased accordingly.
02
The active layout of the industrial chain company
The application of new technologies must first break through the technical difficulties, and large tonnage die casting machines are one of them.
The research report of Soochow Securities shows that the die casting of automobile parts of different sizes requires the corresponding tonnage die casting machine to achieve. According to the calculation of the data disclosed by each company, from the aluminum alloy shell (upper limit 1600T) to the body structure parts (shock -reduction cylinder/longitudinal beam/A/B pillar, etc.) (upper limit 4400T), the locking force of the required crusher continues Ascend, the average high-pressure die-casting machine is between 1000-4400T. The larger volume of products requires a larger tonnage die -casting machine. From the current public information, the die -casting machine required for integrated die -casting is basically above 6000T.
Li Jin Technology (0558.HK) is the main supplier of large tonnage die -casting machines. In 2018, the IDRA of Lichen Technology launched a 6000T ultra -large tonnage die -casting machine and supplied Tesla in 2020, which opened the prelude to the oversized die -casting machine. Since then, Li Jin Technology has completed the delivery of 6800T, 7200T, and 9000T die -casting machines, and has signed a 12000T oversized die -casting with Guangdong Hongtu (002102.SZ).
In addition to Lizhi Technology, Hai Tian Metal of A -share Haitian Seiko is in June last year. Tongxsheng (603305.SH), Merida Technology, and Huizhen Precision Signed a strategic cooperation agreement for large -scale die -casting machines and delivered it in the same year. The first 8800T die -casting machine. The A -share Betting Plastic Machine Leader (300415.SZ) also released a 7000T ultra -large die -casting machine in May this year, and has established a strategic cooperation with FAW casting a 9000T die -casting machine.
The listed companies that purchase die -casting machines are not only Guangdong Hongtu and Xusheng shares, but Wencan (603348.SH) is at the forefront in the field of integrated die casting in China.
Public information shows that Wencan has two 6000T die -casting machines and 2 units of 9000T in 2021. This year, there will be 7 large tonnage die-casting, including 4 die casting machines of 6000-7000T and 3 die casting machines of 9000T. In terms of mass production, Wen Can completed the 6000 Half -section rear floor trial production in November last year, and the 9000T integrated die casting has also been completed. In the 2021 annual report, Wen Can shares said that it has obtained new domestic order orders and will enter the mass production stage this year. In addition, in February this year, Takopu Group (601689.SH) held a grand offline ceremony for the successful mass production of 7200T integrated large die -casting rear cabin; Aikodi (600933.SH) had previously announced that it was planned to purchase 4 6000T+die casting. Machine; Quanfeng Automobile (603982.SH) is expected to complete 7 large -scale die -casting equipment installation and debugging by the end of 2022; June Langtai (605133.SH) signed an agreement with Li Jin Group to purchase the first batch of 3 sets of the first batch of 3 sets from Li Jin 9000T ultra -large die -casting unit, subsequent purchase will be added according to the project progress.
Materials are the key to integrated die casting.
Thermal treatment is usually a process that improves the intensity of aluminum pressure castings. However, because the size of the integrated die -casting products is large, thermal treatment will cause the product to form a variable. Therefore, integrated die -casting products urgently need heat -free alloy. At present, the United States Aluminum Corporation, German Rhein Corporation, Tesla, and the domestic Light China Group and Shanghai Jiaotong University Light Alloy Center have all developed corresponding heat -free treatment alloys.
Among them, Lizhong Group began the research and development of the alloy project in 2016. In 2020, it applied for and obtained a national invention patent certificate, breaking the product monopoly and technical blockade of foreign countries in this field. Shuaiyi Chi Group's heat -free treatment alloy materials have been verified by Weilai Automobile, and Guangdong Hongtu has also developed three types of high -strength, high tough -cast aluminum alloy materials with independent intellectual property rights. As well as
03
No one can retreat during the change
Under the lightweight trend of new energy vehicles, the active promotion of the OEM means that integrated die casting is the general trend. As a new technology for changing traditional automobile manufacturing technology, the emergence of integrated die casting makes automobile parts, especially structural parts, such as Mang Mang.
The cost saved by integrated die casting is the source of profit for some component companies.
In the past, there were many types of structures and different shapes of a car. They could be distributed to many manufacturers. Everyone "drink a pot of porridge together." The integrated die casting is a large structural part. Considering the special nature of the car, it is difficult to distribute the same structure to multiple companies to operate, and the cooperation between the OEM and suppliers has always been relatively stable. In other words, if the layout of integrated die -casting is slow, it may "drink Northwest Wind" in the future.
This is not just some links, but for most automotive component companies. The current integrated die casting is still in the early stages of development. With the advancement of technology, it may not only be the backplane of the car, including the front plate, A/B/C/D pillar, front enclosure and other body structures, as well as the three electricity boxes such as battery boxes and other tri -electricity boxes. The production process of system products may be restructured. No one knows when it will be his turn, and only what he can do is actively layout.
Not only that, the integrated die casting makes the car manufacturing process easier, is it a variable in the future whether the OEMs personally operate or give it to parts companies to participate in the future. If more and more OEMs choose to participate in person, the space left to component companies may be smaller. In contrast, the opportunity for large die -casting machines and heat -free alloy materials may be more certain.
Of course, after all, it is still the beginning of the development of the integrated die casting. How will the future industries evolve in the future. For parts and components, there may be no better way except embrace integrated die casting.
Note: The above content is for reference only, and it is not used as a transaction advice.
Author of this article | Zhang He Source | Yingcai Magazine
- END -
[Ten Years@Every Struggle] "Great Power Craftsman" on the pliers: Gan Dang "Wo Di" educate newcomers

Li Kaijun at work. (Data Map) IntervianEditor's note: Every Chinese who work hard ...
Holgos exported commodity vehicles increased by 128% year -on -year
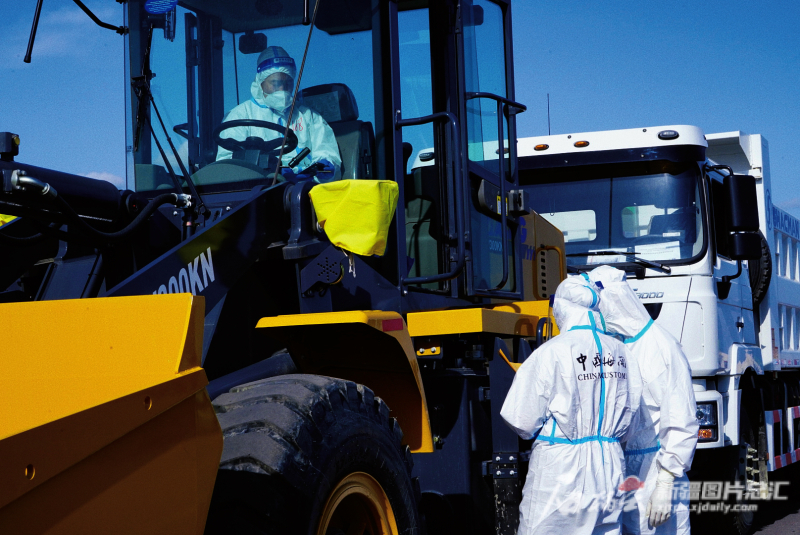
On June 8th, Holgos Customs officers checked vehicle information to the upcoming d...